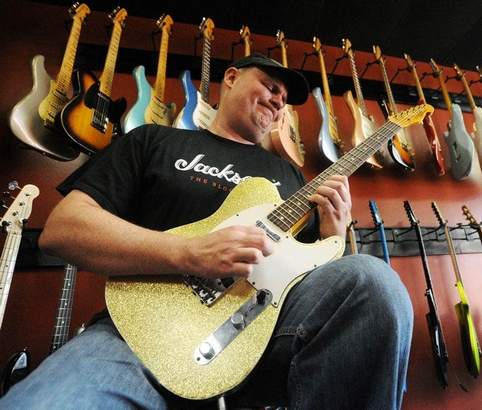
Bass Guitar Shopping on a Budget
When last we met, I told y’all of my plan to check out beginner basses. Well, as I’ve dug deeper into the subject, I’m finding that there are a LOT of good basses out there […]
When last we met, I told y’all of my plan to check out beginner basses. Well, as I’ve dug deeper into the subject, I’m finding that there are a LOT of good basses out there […]
An interesting debate was brought before our attention and felt we should pass it along to you good folks. How does the Gibson Les Paul compare to the Epiphone Les Paul when Epiphone is owned […]
Schecter Guitar Research have officially joined forces with Disturbed guitarist, Dan Donegan. Dan first debuted his signature guitar at the 2009 winter NAMM show. While I’m not a huge fan of Schecter, I was excited […]
Whether its the hands of a sculpture, the pen of a writer, or a voice of a singer, the ability to shape an artistic medium contributes wildly to the captivating nature of art. Nowhere is […]
The Ibanez JS2PRM is an extremely unique and extremely rare instrument in the guitarworld. The JS2PRM—PRM stands for (Premium Rock Mirror)—which is a high-tech finish that was designed to look as if it was carved […]
I’ll admit it. I love pop metal: Bon Jovi, Poison, Motley Crue, Def Leppard. Bring on the cheese. I’m in. Despite the fact that much (though not all) of the music was awful, I still […]
Hello Gear-Vault readers, ’tis the season for that wonderful eggnog, beer and rock ‘n roll! Nothing like getting a few extra days off from work and/or school to spend time with family and loved ones […]
You have just started to play guitar or you are still learning it and having a hard time learning it. Don’t worry even the guitar geniuses went through same phase once. You can achieve success […]
The Dream Of Building Your Very Own Cigar Box Guitar Our existence in the 21st Century has taken on a disposable quality that probably won’t be much admired by future historians. Look at us. Every […]
Call them the biggest of custom shops or the smallest of production plants; either way, Hamer knows how to put together some fine guitars. Even their most affordable instruments reveal an attention to detail you […]
Copyright © 2008 GEAR VAULT · NASHVILLE, TN